Innovative Techniques in Stainless Steel Fabrication
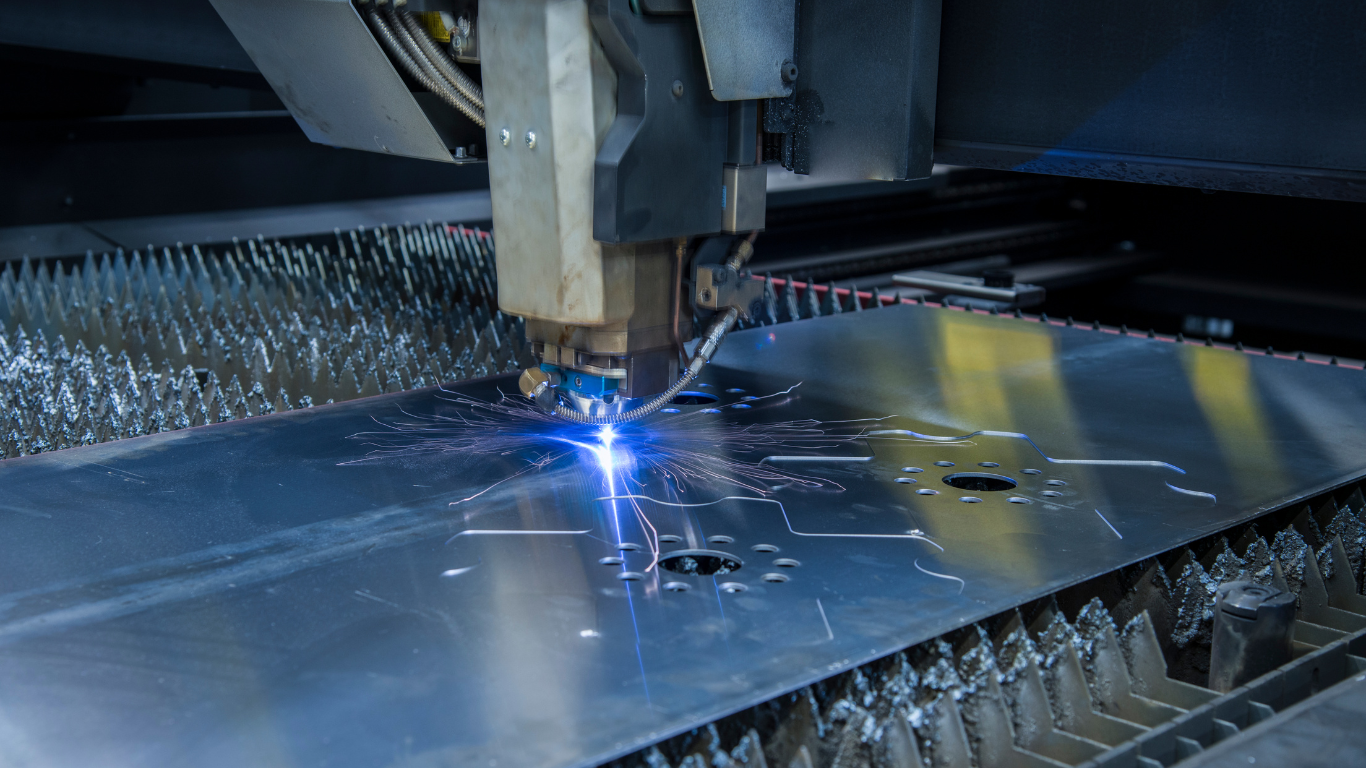
Stainless steel fabrication has come a long way over the years, driven by advancements in technology and the need for more efficient, precise, and high-quality manufacturing processes. As industries continue to evolve, so do the techniques used in stainless steel fabrication. In this article, we’ll explore some of the most innovative techniques that are transforming the stainless steel fabrication landscape.
1. Laser Cutting
Laser cutting has revolutionized the way stainless steel is cut and shaped. This technique uses a high-powered laser beam to cut through the metal with incredible precision. The benefits of laser cutting include:
- Accuracy: The laser beam can create intricate shapes and designs with minimal errors.
- Speed: Laser cutting is faster than traditional cutting methods, reducing production time.
- Minimal Waste: The precision of laser cutting minimizes material waste, making it a cost-effective option.
2. Water Jet Cutting
Water jet cutting is another advanced technique used in stainless steel fabrication. This method involves using a high-pressure stream of water, often mixed with abrasive particles, to cut through the metal. Key advantages of water jet cutting include:
- No Heat-Affected Zones: Unlike laser cutting, water jet cutting does not generate heat, preventing any thermal distortion of the metal.
- Versatility: It can cut through a wide range of materials and thicknesses.
- Environmental Benefits: Water jet cutting produces no hazardous waste, making it an environmentally friendly option.
3. Robotic Welding
Robotic welding has become increasingly popular in stainless steel fabrication due to its precision and efficiency. Robots are programmed to perform complex welding tasks, offering several benefits:
- Consistency: Robotic welding ensures uniform welds, reducing the risk of human error.
- Speed: Robots can work continuously without fatigue, speeding up the welding process.
- Safety: Automated welding reduces the risk of accidents and exposure to hazardous fumes.
4. 3D Printing
3D printing, also known as additive manufacturing, is making waves in the stainless steel fabrication industry. This technique involves layering material to create complex shapes and structures. The advantages of 3D printing include:
- Design Flexibility: 3D printing allows for the creation of intricate and custom designs that would be difficult to achieve with traditional methods.
- Reduced Waste: Material is added layer by layer, minimizing waste.
- Rapid Prototyping: 3D printing enables quick production of prototypes, speeding up the development process.
5. Hydroforming
Hydroforming is a process that uses high-pressure hydraulic fluid to shape stainless steel into complex forms. This technique is particularly useful for creating lightweight, high-strength components. Benefits of hydroforming include:
- Uniformity: The process ensures even distribution of material, resulting in consistent thickness and strength.
- Efficiency: Hydroforming can create complex shapes in a single step, reducing the need for multiple manufacturing stages.
- Material Savings: The technique optimizes material usage, reducing waste.
6. Electrochemical Machining (ECM)
Electrochemical machining (ECM) is a precision technique that removes metal using an electrochemical process. This method is ideal for hard-to-machine materials like stainless steel. Key benefits include:
- Precision: ECM can produce highly accurate and complex shapes with excellent surface finishes.
- No Thermal Damage: As ECM does not generate heat, there is no thermal distortion or stress on the material.
- Tool Longevity: The process does not wear down the tool, extending its lifespan.
7. CNC Machining
Computer Numerical Control (CNC) machining is a highly automated technique used in stainless steel fabrication. CNC machines are programmed to perform precise cuts, drills, and other operations. Advantages include:
- Accuracy: CNC machines offer high precision and repeatability.
- Complexity: They can handle complex designs and shapes.
- Efficiency: Automation speeds up production and reduces labor costs.
8. Plasma Cutting
Plasma cutting uses a jet of hot plasma to cut through stainless steel. It is an effective method for cutting thick materials. Benefits include:
- Speed: Plasma cutting is faster than traditional cutting methods.
- Versatility: It can cut through various thicknesses and types of metal.
- Quality: Produces clean cuts with minimal finishing required.
9. Powder Coating
Powder coating is a finishing technique that involves applying a dry powder to stainless steel and then curing it under heat. This process provides a durable and attractive finish. Advantages include:
- Durability: Powder coating is resistant to chipping, scratching, and fading.
- Environmental Friendliness: It produces fewer VOCs (volatile organic compounds) compared to liquid coatings.
- Variety: Available in a wide range of colors and textures.
10. Bending and Forming
Advanced bending and forming techniques, such as roll forming and press braking, allow for the creation of complex shapes and structures from stainless steel. These methods offer:
- Precision: Modern equipment ensures accurate and consistent bends.
- Efficiency: Automated processes reduce production time and costs.
- Flexibility: Capable of handling a variety of shapes and sizes.
Conclusion
Innovative techniques in stainless steel fabrication are transforming the industry, enabling the creation of more complex, precise, and high-quality products. From laser cutting and 3D printing to robotic welding and hydroforming, these advancements are driving efficiency, reducing waste, and enhancing the overall capabilities of stainless steel fabrication. As technology continues to evolve, we can expect even more groundbreaking techniques to emerge, further pushing the boundaries of what is possible in stainless steel fabrication.